Compared to processes such as plating and surface treatment, cleaning seems to be an insignificant step. Most of you may don’t consider cleaning a worthwhile investment, for cleaning only costs time and money. But in fact, cleaning is crucial to product quality and has a great impact on the subsequent process. It is necessary to analyze the reasons why cleaning is so important.
Before heat treatment, the surface of the workpiece usually looks clean and is free of defects on visual inspection. However, in processes after heat treatment (such as nitriding), problems caused by substandard surface cleanliness are revealed. Rework of defective products is costly in terms of time and money, and defective products cannot be reworked in most cases.
If case of any one of such problems, we should investigate the causes as soon as possible. Mechanical and equipment causes should be checked first: type of material, shape of parts, nitriding furnace procedure, and mechanical processing. If these factors can be ruled out, the defect is usually caused by an invisible diffusion-blocking layer on the surface of the workpiece, which means that it is some residue on a visually clean part surface that causes the defect.
Prior to heat treatment, the part undergoes multiple processes, resulting in surface changes. There are two main types of changes.
Mechanical changes: deformation; extrusion; grinding.
Chemical changes: phosphate layers (e.g. zinc phosphating to assist in drawing); anti-corrosion compounds; chlorine, phosphorus or sulfur may be contained in cooling lubricant, saponification fluid, oil and other additives; surface crack detection reagent.
How to clean the workpiece to ensure the surface cleanliness?
Usually 95-99% water with 1-5% cleaning agent is used to clean the workpiece, and the water quality is very critical. Impurities in the water such as calcium, magnesium, sodium, potassium, and chloride can remain on the surface of the workpiece after drying to form a diffusion barrier, so deionized water with a conductivity of up to 50 µS/cm should be used to prevent problems during cleaning.
The aqueous cleaning system contains two types of components: main cleaning agent and surface active agent.
Main cleaning agent: It contains inorganic or organic substances, such as alkali, phosphate, silicate, and amine. It can adjust the pH, provide electrical conductivity, and saponify grease.
Surface active agent: It contains organic substances, such as alkyl benzene sulfonates and fatty alcohol ethoxylates, and plays the roles of dissolving and dispersing oils and fats.
The four important parameters of aqueous cleaning are cleaning fluid, cleaning time, cleaning temperature and cleaning method.
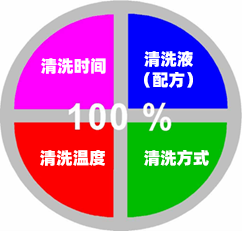
1. Cleaning fluid
The cleaning fluid should adapt to the part (type of material), current impurities and subsequent surface treatment.
2. Cleaning time
The cleaning time depends on the type and amount of contamination and may depend on the given sequence of the cleaning line so as not to interfere with subsequent work steps.
3. Cleaning temperature
Higher cleaning temperature will reduce the viscosity of the oil and melt the grease, making it faster and easier to remove these substances.
4. Cleaning method
Different functions are introduced through the cleaning equipment, such as: tank circulation, overflow, spraying, and ultrasonic. The cleaning method depends on the type and shape of part, contamination and available cleaning time.
These four parameters must be adjusted to the actual situation. More energy supply (mechanical, thermal or chemical) or longer treatment time will improve the cleaning effect. In addition, a stronger flow of cleaning fluid will improve the cleaning effect at low temperatures.
It is worth noting that some of the contaminants are extremely well bonded and cannot be removed by cleaning. Such contaminants can usually only be removed by processes such as grinding, sandblasting, and pre-oxidation.
Post time: Jun-24-2022